What is an explosion-proof industrial vehicle ?
1、Overview
Explosion-proof industrial vehicles is a typical combination of explosion-proof electrical equipment. Explosion-proof industrial vehicles, according to the drive power classification, is divided into battery-type explosion-proof vehicles and internal combustion engine explosion-proof vehicles; according to the use of functional classification, is divided into counterbalanced explosion-proof forklift and flatbed explosion-proof trucks and so on.
For battery-type vehicles, power-driven device is a DC motor, powered by the battery pack, it is a small limited electrical network, not only an independent power supply, but also the use of a variety of electrical appliances, such as electric motors, control switches, signal indicators and lighting fixtures, etc.; for the internal combustion engine-type vehicles, the power-driven device is a reciprocating internal combustion engine, and in addition to set up a small battery pack and the relevant control unit. The power driving device is a reciprocating internal combustion engine, in addition to a small battery pack and related control units. Whether it is a battery-type vehicles or internal combustion engine-type vehicles, but where the production of explosion-proof industrial vehicles, people must take appropriate explosion-proof technical measures for its constituent parts.
According to the explosive hazardous areas of the zoning and industrial site conditions, explosion-proof industrial vehicles should be adapted to the explosive hazardous areas in Zone 1, Zone 2 and the existence of these areas in the Ⅱ A, Ⅱ B and Ⅱ C, T1 ~ 4 groups of combustible gases in the comprehensive level of protection (explosion-proof level of safety), should have Gb level of equipment protection.
Thus, this explosion-proof type of industrial vehicles can be run in the explosive hazardous areas in Zone 1 and Zone 2, as a short-distance transportation.
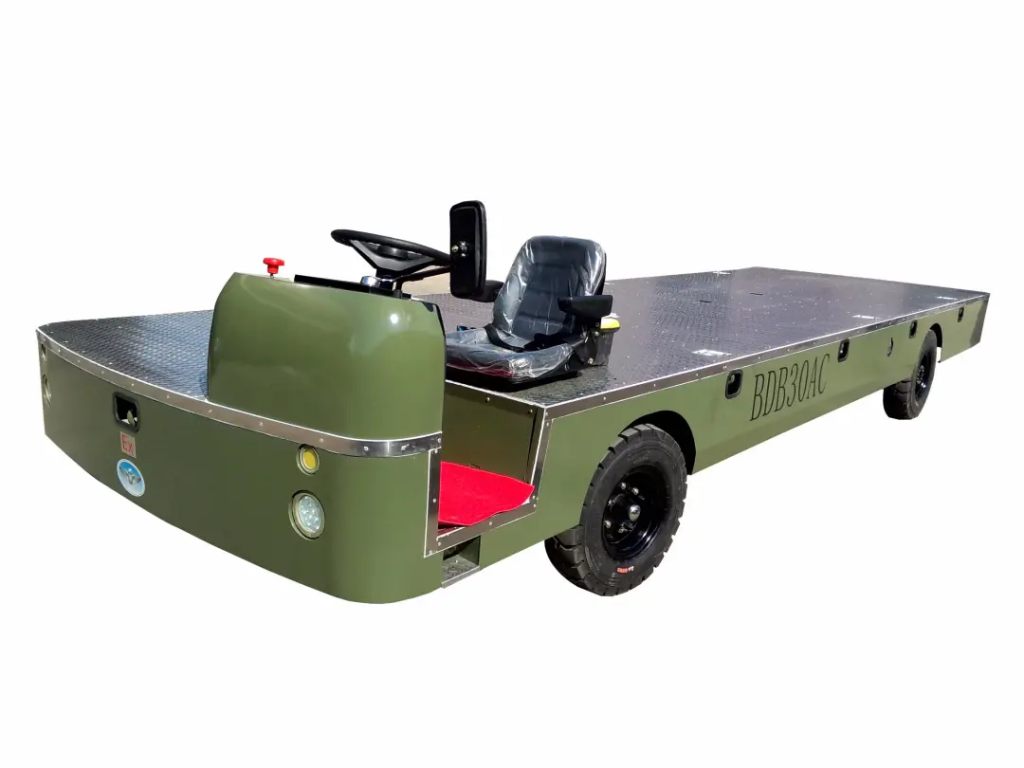
2. explosion-proof structure and safety requirements
According to the explosion-proof safety level of the explosion-proof industrial vehicles, we will take and put forward the corresponding safety measures and safety requirements, to ensure that this kind of industrial vehicles in explosive hazardous places will not become the ignition source of combustible gases.
(1) power drive
For battery-type explosion-proof vehicles, the power driving device is an explosion-proof DC motor. Flame-proof DC motor should meet the appropriate requirements.
For internal combustion engine explosion-proof vehicles, the power drive is explosion-proof reciprocating internal combustion engine. Explosion-proof reciprocating combustion engine should meet the appropriate requirements.
(2) Electrical unit
In the explosion-proof industrial vehicles used in the explosion-proof electrical unit, can be in addition to the “n” type explosion-proof type (Ge class) other than all other explosion-proof type of electrical equipment (Ga and Gb class), such as intrinsically safe “i”, explosion-proof type “d”, explosion-proof type “d”, explosion-proof type “d”, explosion-proof type “d”, explosion-proof type “d”, explosion-proof type “d”, explosion-proof type “d”, explosion-proof type “e” and “f”. “d”, increased safety type ‘e’ and cast-in type ‘m’. The power supply used in this type of vehicle is a special type of explosion-proof battery pack that is allowed to operate in Zone 1 in explosive hazardous areas.
3. Cables and installation
On explosion-proof industrial vehicles, the designer should use insulated copper-core flexible cables. The current-carrying capacity of the cable should be such that the temperature generated during the passage of the rated current of the relevant electrical equipment on the vehicle is not higher than the temperature value of the temperature group or the permissible temperature value of the insulating material. The cables shall be capable of withstanding a voltage withstand test voltage of at least 500 V (I.F.).
The cable should be installed on the vehicle to avoid high temperature parts and moving parts, should be firm and reliable, and shall not be loosened and swung during the operation of the vehicle.
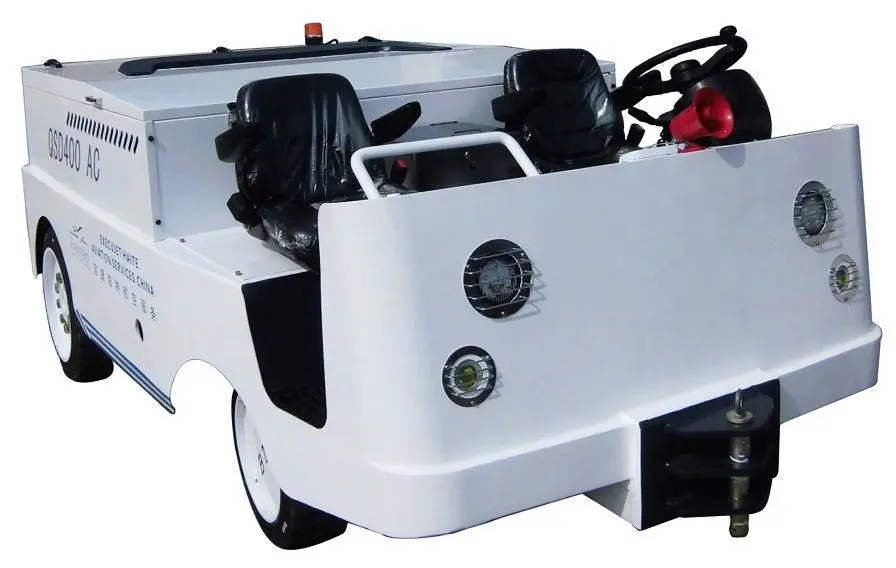
4. Protection devices
For battery-type explosion-proof vehicles, designers should set up overcurrent protection links in the electrical circuit to prevent excessive current damage to the battery pack and cause impermissible dangerous temperatures.
Typically, the overcurrent protective device should be set to a value that effectively cuts off 1.1 times the value of the starting current when the vehicle is started on the design ramp at the standard design load condition. The use of fuses as overload protection is not considered to be overcurrent protection as described herein.
In the case of combustion-engine type explosion-proof vehicles, the designer provides an automatic alarm device and an automatic stop device in the reciprocating combustion-engine protection system to prevent abnormal conditions and impermissible dangerous temperatures of the combustion-engine during the operation of the vehicle.
As for the electrical protection, usually the fuse (explosion-proof) protection can be used.
5. Electrical insulation
In explosion-proof industrial vehicles, all explosion-proof electrical units and electrical connections must be kept well insulated from the metal components of the vehicle body, even intrinsically safe circuits are not allowed to connect with the vehicle body.
The operator should regularly check the insulation resistance of the vehicle. Under normal operating conditions, this resistance should not be less than 0.5MΩ.
6. Transmission/Braking System
On explosion-proof industrial vehicles, all components in the transmission/braking system should operate flexibly and be well lubricated.
① In the transmission system, the clutch should meet any of the following requirements:
-Hydraulic clutches, torque converters, hydrostatic drives and oil-cooled clutches should comply with the temperature group.
-Mechanical clutches should comply with the requirements of the temperature group and should also be protected against mechanical sparks caused by friction and collision during normal operation.
-Friction clutches should be placed in a lubricating fluid or protected by a flameproof housing.
② In a braking system, the brake should meet either of the following requirements:
-The brake should be placed in a lubricating fluid or protected by a flameproof enclosure.
-The brake should use non-metallic materials and cast iron, or non-metallic materials and materials with the same friction properties as cast iron to make the friction partner.
It should be noted here that the non-metallic compound should not contain more than 40% metal. The characteristic value of the size of the metal particles or filaments should not exceed 500 μm.
When the surface temperature of the brake may exceed the temperature value of the temperature group, the designer should configure a temperature monitoring device. The temperature monitoring device should be activated when it detects that the temperature is 10 K below the temperature value for the temperature group, stopping the vehicle from continuing operation.
The temperature of the hydraulic system should not exceed the temperature value of the corresponding temperature group.
7. Static electricity
In explosion-proof industrial vehicles, the parts that may normally generate and accumulate static charges are tires, seats and steering wheels made of plastic materials, and other auxiliary parts made of plastic or rubber materials.
Experimental studies have pointed out that an ordinary type industrial vehicle operating at rated speed on a gravel road generates an electrostatic voltage of 2.7 kV on its tires and that this electrostatic charge is negatively polarized. Experiments have shown that the distribution of electrostatic charge on tires is not uniform.
In order to prevent the generation and accumulation of electrostatic charges, designers must use some anti-static measures on explosion-proof industrial vehicles.
(1) tires
Tires should be anti-static type tires. In the manufacture of tires in the rubber material to add appropriate conductive agent, you can achieve the effect of anti-static.
The surface resistance of the material used in the manufacture of antistatic tires should not exceed 10 mΩ (50% relative humidity) or 1.0 mΩ (30% relative humidity) when measured under the specified test conditions (see Chapter 2).
For vehicles with a rated operating speed of not more than 6km/h, the inspector may not require the surface resistance value of the tire.
(2) Plastic materials or (and) rubber materials
Plastic materials or (and) rubber materials used on explosion-proof industrial vehicles, when they may be rubbed during normal operation of the vehicle, shall comply with any of the following provisions and requirements:
① The surface resistance measured under the specified test conditions should not exceed 10mΩ (50% relative humidity) or 1.0mΩ (30% relative humidity).
② The surface area should not exceed 100cm² (Class IIA and IIB) or 20cm² (Class IIC).
③ For plastic materials or rubber materials with embedded metal parts, the dielectric strength breakdown voltage measured during the test in accordance with the method specified in the national standard GB/T 1408.1 “Test Method for Electrical Strength of Solid Insulating Materials under Industrial Frequency Test” should not be greater than 4kV.
(3) potential balance
In explosion-proof industrial vehicles all metal parts with an area greater than 100cm² must be connected to the frame in order to maintain the potential balance of all parts of the vehicle.
If these parts are in “metallic” contact with each other, there is no need to bridge them with a special conductor.
8. Mechanical sparks
Under normal operating conditions, explosion-proof industrial vehicles on the part of the friction and collision with the outside may occur, should be used in the friction and collision does not produce mechanical sparks in the material cladding.
For example, copper, copper-zinc alloy, copper-beryllium alloy, stainless steel and other materials can be used to prevent the generation of mechanical sparks. In a forklift one can cover the forks with brass or stainless steel.
If non-metallic materials (e.g., plastic or rubber) are used to prevent mechanical sparking, designers should consider their antistatic properties. Sometimes, people often use rubber sheet padding in the handling vehicle on the platform, to prevent the goods and platform collision and friction; of course, people can also use friction and collision does not produce sparks when the metal plate for such protection.
In the explosion-proof industrial vehicles on the rotating parts and the neighboring parts should be maintained at a sufficient distance between.
9. Temperature limitations
Regardless of the type of explosion-proof electrical equipment, the temperature limit is an important safety indicator. For explosion-proof industrial vehicles, used to determine the temperature of its temperature groups are many, for example, the brake temperature of the friction plate in the brake, DC motor or reciprocating internal combustion engine surface temperature, and so on.
The temperature of all heated parts of the vehicle should not exceed the temperature value of its temperature group and the stabilized operating temperature value of the material used.
In summary, as long as the proper adoption of the above explosion-proof structure and safety requirements, you can realize the explosion-proof safety performance of industrial vehicles.
It should be pointed out here is that in the explosion-proof industrial vehicles do not set combustible gas alarm devices. In explosion-proof industrial vehicles set combustible gas alarm device as its explosion-proof technical measures is a pseudo-proposition, because, in accordance with the above explosion-proof structure and safety requirements for the design and production of explosion-proof industrial vehicles to run in explosive gas environments, assuming that the setting of the combustible gas alarm device, once the alarm device alarm vehicle stops running, the explosion-proof structure and safety requirements lose meaning; once the alarm device alarm malfunction, the vehicle continues to run; once the explosion-proof structure and safety requirements; once the explosion-proof structure and safety requirements. Alarm device alarm failure, the vehicle continues to run is still safe, then the alarm device is not necessary to set up. This should cause the designers and operators enough attention.