Some knowledge about explosion-proof fans
Explosion-proof fan
When the fan is conveying flammable and explosive gases and dusts, static electricity and sparks are extremely dangerous factors, which may cause explosions and other safety accidents if special handling measures are not taken.
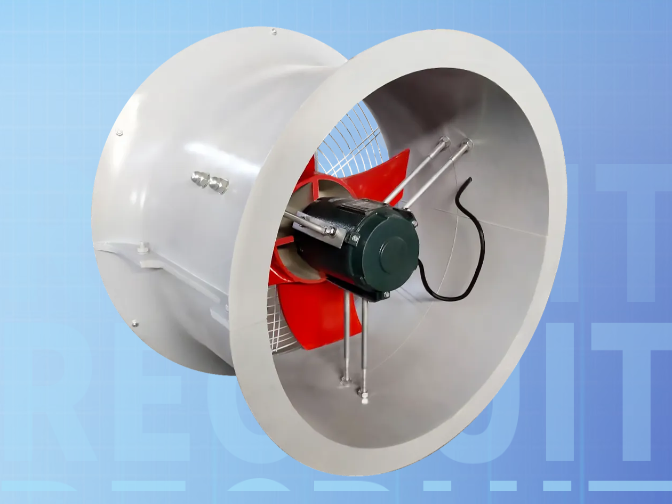
1 How to confirm the explosion-proof fan?
To confirm exactly whether the fan is explosion-proof, you can judge through the following series of methods: first, check whether the explosion-proof fan shell or electrical control box has an explosion-proof mark. This symbol includes details of the explosion-proof class, the type of gas or dust to which it applies, the type of explosion-proofing, etc. In China, these standards are set by the AQSIQ. In China, these standards are set and promulgated by the AQSIQ.
Secondly, it is important to have an in-depth understanding of explosion protection ratings. Typically, explosion-proof ratings are expressed in two standards, IP and EX. The IP standard is primarily concerned with the level of protection, while the EX standard is specifically for explosion-proof equipment. In the EX standard, the next two digits represent the explosion-proof level, for example, in EXdIICT6, “d” represents the explosion-proof shell, “II” represents the applicable type of gas or dust, “CT6” represents the temperature rise limit. The “CT6” indicates the temperature rise limit.
Furthermore, it is important to recognize the explosion-proof marking of the fan and the corresponding certification. The explosion-proof marking is generally divided into Ex and D. The Ex marking is a common European and international explosion-proof marking, while the D marking is specific to Germany. In addition, explosion-proof fans also need to pass the corresponding explosion-proof certification, such as the European Union’s ATEX certification and China’s CCC certification.
At the same time, it is important to fully understand the environment and application requirements of explosion-protected fans. Explosion-proof fans are mainly used in flammable and explosive environments, such as chemical plants, petrochemicals, coal mines and so on. When choosing an explosion-proof fan, you need to understand the environmental conditions in detail, including the grade of gas, liquid, dust, etc., temperature, humidity and other factors.
Finally, it is necessary to determine the appropriate explosion-proof grade (e.g. Exd, Exe) as well as the protection grade (e.g. IP54, IP65) according to the specific environmental conditions and working requirements. And, also consider the materials used for the fan, such as aluminum alloy, stainless steel, etc., as well as the corrosion resistance and high temperature resistance of these materials.
2 Explosion-proof fan for what places
Explosion-proof fans are widely used in many industrial areas where there is a need to prevent explosions caused by sparks or high temperatures. The following are some common areas of application for explosion-proof fans:
Chemical plants: There are many flammable and explosive substances in the chemical industry. Explosion-proof fans are used to ensure that no sparks or high temperatures are generated when handling, mixing or conveying chemicals, reducing the risk of fire or explosion.
Oil and gas industry: Explosion-proof fans are used to handle and transport oil and gas in refineries, oil and gas drilling platforms, tank farms, etc. to ensure safe operation in flammable gas environments.
Mining: In mining operations, because of the presence of flammable gases or dust, explosion-proof fans are used to ventilate, discharge exhaust gases and ensure that no sparks are generated to trigger an explosion in the mine.
Pharmaceutical Manufacturing: In the pharmaceutical industry, explosion-proof fans are used to handle medicines, powders or solutions and to ensure that there are no accidental explosions during the production process.
Paint and lacquer industry: Explosion-proof fans are used in paint and lacquer production lines to prevent fires or explosions caused by the build-up of solvent vapors or particulate matter.
Food processing: Explosion-proof fans are used to ensure safety during food production in the food processing industry, especially in environments where dust or flammable gases need to be handled.
Overall, explosion-proof fans play an important role in a variety of industrial sectors and are used to ensure safe operation and production in flammable and explosive environments.
3 What is the principle of the explosion-proof ventilator?
The explosion-proof principle of the explosion-proof ventilator is the ability to avoid possible sparks, arcs and dangerous temperatures during its operation or work, thus ensuring that its operation cannot ignite the surrounding explosive environment.
The driving motor of the explosion-proof ventilator adopts the explosion-proof motor, and the material of the impeller and the casing adopts the paired material that meets the requirements of explosion-proof. The assembly of the casing and impeller of the explosion-proof ventilator, the protection of the air inlet and outlet, the influence of the load on the temperature rise of the motor, and the protection grounding device, etc. should also meet the requirements of the explosion-proof standard.
There are many types of explosion-proof ventilators, such as explosion-proof axial fans, explosion-proof centrifugal fans, explosion-proof side-wall fans, explosion-proof roof fans and so on.
4 General requirements for explosion-proof fans
I. Explosion-proof ventilator product performance requirements
1. In the rated speed and the specified flow range, the deviation between the measured pneumatic performance of the ventilator and the specified pneumatic performance shall meet the following provisions:
a) Under the specified flow rate, the pressure value of the machine number less than or equal to No.10 ventilator does not exceed -8 %~+ 5% of the specified value; the pressure value of the machine number greater than No.10 ventilator does not exceed -5%~+5% of the specified value.
b) The efficiency of the ventilator shall not be less than 8% of its corresponding point efficiency.
2. The noise of the ventilator in the best efficiency of the working point than the A sound level Las value should be consistent with the provisions of JB/T 8690.
3. The bearing temperature rise and support vibration speed of the ventilator shall comply with the following provisions:
a) The bearing temperature measured on the bearing surface shall not be higher than the ambient temperature by more than 40 ℃.
b) The effective value of the vibration velocity shall not exceed 4.6 mm/s for rigid bearings and 7.1 mm/s for flexible bearings
II. Structural requirements
1. Basic design requirements
a) Under the specified working conditions, the ventilator and auxiliary equipment shall be designed for a service life of at least 10a (except for wearing parts) and a safe operation time of not less than 18,000 h before the first overhaul.
b) The critical speed of the rigid shaft of the ventilator shall be 1.3 times the maximum working speed.
c) The basic type, size parameters and performance curve of the ventilator should be consistent with the provisions of GB/T 3235.
d) Ventilator in the structure, the requirements of the rotating parts and adjacent static parts to avoid friction, in order to prevent the generation of sparks. Other aspects such as structure, type, strength, stiffness, etc. should be met: axial flow ventilator should be in line with the relevant provisions of JB/T 10562, centrifugal ventilator should be in line with the relevant provisions of JB/T 10563, and other ventilators should be in line with the provisions of the relevant standards.
2. Impeller
a) The impeller of the ventilator shall be subjected to over-speed test, and the impeller shall be operated at a speed of not less than 110 % of the maximum working speed for a period of not less than 2 min, and in accordance with the provisions of JB/T 6445.
b) The impeller should be balanced and corrected, and the balance quality level should be in accordance with the provisions of JB/T 9101.
c) impeller riveted parts rivets with through-hole diameter according to the relevant provisions, riveting quality requirements should be in line with the provisions of JB / T 10214.
III. Main parts
a) When the impeller of the ventilator is made of aluminum alloy, the air inlet chamber and casing must be made of carbon steel.
b) ventilator impeller with steel materials, centrifugal ventilator inlet chamber mouth ring and rivets must be used brass or aluminum; axial flow ventilator steel casing corresponding to the impeller must be used in the parts of the brass or aluminum ring and the corresponding rivets.
c) The use of other materials, should be used to rotate and static parts of the material does not produce sparks, technical requirements should be consistent with the provisions of JB / T 10562 and JB / T 10563.
IV.
a) Casting requirements Casting quality should be in accordance with the appropriate provisions.
b) Requirements for riveted parts Welding quality, riveted parts manufacturing, and other welding requirements shall be in accordance with the appropriate provisions.
V. Assembly requirements
a) centrifugal ventilator inlet chamber mouth ring and impeller inlet radial clearance along the circumference should be uniform, machine number less than or equal to №.10 ventilator radial unilateral clearance for 2.5 mm ~ 4 mm, machine number greater than No. 10 ventilator radial unilateral clearance for (0.15% ~ 0.4%) D impeller diameter, but the minimum radial unilateral clearance shall not be less than 2.5 mm, axial overlap length of (0.8% ~ 1.2%) D impeller diameter. ~1.2 % ) D impeller diameter.
b) axial flow ventilator casing and impeller radial clearance should be uniform, machine number is less than or equal to No.10 of the ventilator radial unilateral clearance of 2.5mm ~ 4mm, machine number is greater than No.10 of the ventilator radial unilateral clearance (0.15% ~ 0.35%) D impeller diameter, but the minimum radial unilateral clearance shall not be less than 2.5mm.
VI. Security requirements
a) Flame-proof motors and supporting electrical accessories used for ventilators shall comply with the corresponding regulations.
b) The surface of the ventilator casing and the surface of the drive assembly shall have a grounding device that meets the explosion-proof requirements and a permanent grounding symbol at the appropriate place.
c) ventilator air intake chamber directly open to the atmosphere, the air intake chamber must be installed with a fixed protection grid (or net) to prevent foreign objects sucked into the ventilator. Protection grid (net) structure design in addition to consider the size of the fan number, the working environment and other factors, should also be considered to add protection grid (net) caused by the airflow resistance is minimized.
d) transmission group, coupling, pulleys, belts and other rotating (transmission) parts should be a safety device shroud, and in line with the provisions of GB/T 19074. Shroud structure should be solid and avoid contact with the rotating parts. In order to avoid the collection of static electricity on the shroud to produce sparks, and the casing of the shroud should be insulated with a reliable grounding device.
e) The rotating parts of the ventilator must be firmly fixed, and there should be measures to prevent loosening (the impeller and the shaft are locked; the bearing seat, bearing box and the motor and the bracket have positioning measures).
f) ventilator when the impeller spindle through the casing, the steel casing of the shaft hole and the shaft through the part should be installed with a stopping aluminum sealing isolation ring; sealing isolation ring bore and shaft with the unilateral clearance of 0.5 mm.