Explosion-proof measures for hazardous chemicals in different states
Chapter I. Prevention of gas explosions
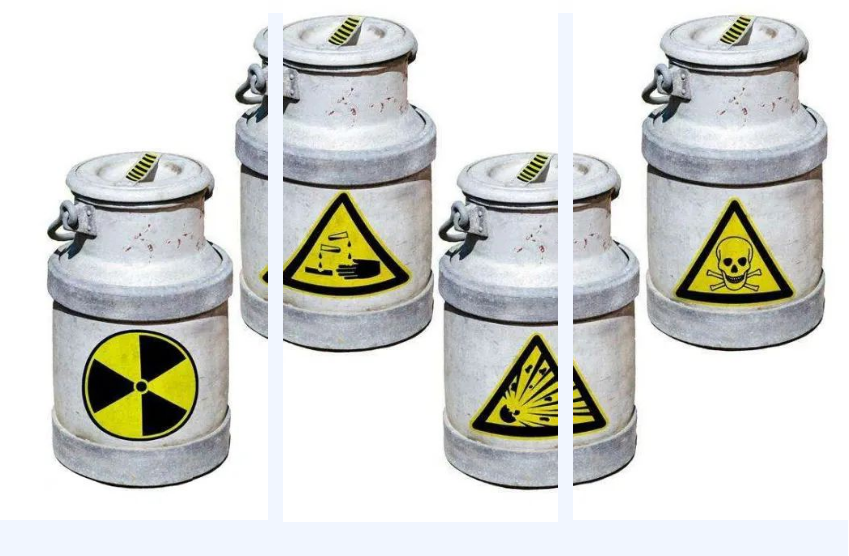
Typically, a fire starts and then gradually spreads and expands, with damage increasing dramatically with time. For the fire, the initial firefighting is still relevant. Explosions, on the other hand, are sudden, and in most cases, the explosion process is completed in an instant, and casualties and material damage are caused in an instant. In addition, the fire may also cause an explosion, because the fire in the open flame and high temperature can cause flammable materials to explode. Such as oil or explosives depot fire may cause sealed oil drums, explosives explosion; some substances at room temperature will not explode, such as acetic acid, in the fire at high temperatures have become explosives may be. Explosions can also cause fires, explosions throw flammable materials may cause large fires, such as sealed fuel oil tanks after the explosion due to the leakage of oil caused by fire. Therefore, in the event of a fire, to prevent the fire into an explosion: when an explosion occurs, but also to take into account the possibility of starting a fire, and take timely preventive and rescue measures.
1. Hazardous characteristics of flammable and explosive gases
(1) Flammable and explosive The main danger of combustible gases is that they are flammable and explosive, and all combustible gases within the explosion limit can ignite or explode when they meet the ignition source, and some combustible gases can be detonated when they meet the action of an ignition source with very small energy. Combustible gases in the air fire or explosion degree of difficulty, in addition to the influence of the size of the ignition source energy, mainly depends on its chemical composition. Chemical composition determines the size of the combustion concentration range of combustible gases, spontaneous combustion point of high and low, the speed of combustion and heat generation.
(2) Diffusivity Any substance in the gaseous state has no fixed shape or volume and can spontaneously fill any container. Gases diffuse very easily because of their large molecular spacing and small interaction forces.
(3) Shrinkability and Expansion The volume of a gas expands and contracts in response to increases and decreases in temperature, and its expansion and contraction is much greater than that of a liquid.
(4) charged by the principle of electrostatic generation can be seen, the friction of any object will produce static electricity. Compressed or liquefied gas is also the case, such as hydrogen, ethylene, acetylene, natural gas, liquefied petroleum gas, etc. from the mouth of the pipe or broken at high speed can produce static electricity, mainly due to the gas contains solid particles or liquid impurities, in the pressure of high-speed spraying with the nozzle to produce a strong friction. Impurities and flow rates affect the generation of fluid electrostatic charges.
Chargeability is one of the parameters for evaluating the fire danger of combustible gases. With the knowledge of the chargeability of combustible gases, corresponding precautionary measures can be taken, such as grounding of the equipment, controlling the flow rate and so on.
2. Explosive limit of the factors affecting
A variety of different combustible gases and flammable liquids and vapors, due to their different physical and chemical properties, and thus have different explosion limits: the same kind of combustible gases or flammable liquids and vapors of the explosion limit, but also is not fixed, by the temperature, pressure, oxygen content, inert media, the diameter of the container and other factors.
3. Basic measures to prevent fire and explosion accidents
Three conditions must be present for a flammable gas to explode:
First, there are flammable gases;
Secondly, air is available and the mixing ratio of combustible gas to air must be within certain limits;
Third, the presence of an ignition source. An explosion cannot occur without one of these three conditions.
Therefore, the principles of preventing combustible gas explosions include: strict control of ignition sources; to prevent the formation of explosive mixtures of combustible gases and air; to cut off the explosion propagation pathway, in the beginning of the explosion in a timely manner to relieve the pressure, to prevent the expansion of the scope of the explosion and the explosion of the pressure rise. The above principles are equally applicable to the prevention of gas explosions, liquid vapor explosions and dust explosions.
(1) the control and elimination of ignition sources cause fire ignition sources are generally open flame, friction and impact, heat rays, high-temperature surfaces, electrical sparks, static sparks, etc., strict control of the use of such sources of ignition, fire and explosion prevention is very necessary.
a. Open flame mainly refers to the production process of heating fire, maintenance of welding fire and other sources of ignition, open flame is the most common cause of fire and explosion, heating flammable materials, we should try to avoid the use of open flames and the use of steam or other heat-carrying body heating.
b. Friction and Impact Sparks may be generated by friction of rotating bearings in the machine, by mutual impact of iron tools, or by striking concrete floors with iron tools, etc. Therefore, bearings should be well lubricated, and steel tools should be used in hazardous places instead of iron tools.
c. Heat rays Ultraviolet light can promote certain chemical reactions: infrared light, although invisible, but a long period of localized heating can also make combustible materials on fire; direct sunlight through convex lenses, circular flasks will be focused, and its focus can be a source of ignition.
(2) Explosion control Most of the damage caused by explosions is very serious, and scientific explosion prevention is a very important task. The main measures to prevent explosions are as follows.
a. Inert media protection in chemical production, used as a protective gas inert gas mainly nitrogen, carbon dioxide, water vapor and so on. Generally need to consider the use of inert media protection in the following cases: flammable solids crushing, screening process and its powder transportation needs inert media protection; processing of flammable and explosive materials system, before feeding, with inert gas replacement to exclude the original gas in the system to prevent the formation of explosive mixtures.
b. System containment Prevent leakage of combustible materials and entry of air. In order to ensure that the system is airtight, hazardous equipment and systems should try to use welded joints, less flange connection: to prevent toxic or explosive hazardous gases from escaping outside the container, negative pressure operating system can be used, for the production of equipment operating under negative pressure, air intake should be prevented: according to the process temperature, pressure and media requirements, the use of different sealing gaskets.
c. Ventilation and replacement of combustible substances to reach the explosion limit. In the case of equipment can not guarantee absolute sealing, should make the plant, workshop to maintain good ventilation conditions, so that the leakage of a small amount of combustible gases can be readily discharged, not to form an explosive gas mixture. When designing the ventilation exhaust system, the density of combustible gases should be considered. In places where combustible gases lighter than air (e.g. hydrogen) are produced and used, exhaust channels such as skylights should be set up on the roof of the plant: when combustible gases are heavier than air, leaking gases may accumulate in low-lying areas such as gutters and form explosive gas mixtures with air, and measures should be taken in these places to exhaust the gases.
d. Installation of explosion containment system Explosion containment system consists of sensors that can detect the initial explosion and pressure-type extinguishing agent canisters, the extinguishing agent canisters through the sensing device action, in the shortest possible time to the extinguishing agent evenly sprayed into the containers need to be protected, the combustion is extinguished, so as to control the occurrence of the explosion. In the explosion encounter system, the explosion and combustion can be detected by itself, and after a certain period of time after the power failure system can continue to work.
Chapter II. Prevention of liquid explosions
Various chemical enterprises, in the production of a large number of flammable, explosive, volatile liquids, if the slightest carelessness in the production and storage process, will cause fire accidents, resulting in casualties and property damage.
1. Fire hazards of flammable and explosive volatile liquids
(1) Combustion and Explosivity The combustion and explosivity of flammable and explosive volatile liquids depends on the flash point and explosion limit. Above the flammable liquid, vapor and air mixture of gas in the event of an ignition source flash instantaneous combustion phenomenon known as flash ignition. In the specified experimental conditions, the surface of the liquid can produce the lowest temperature of flash ignition is called the flash point. Liquid flash ignition, because its surface temperature is not high, the rate of evaporation is less than the combustion rate, the resulting vapors can not replenish the vapors burned off, but only to maintain the instantaneous combustion. Evaporation vaporization process of liquid combustible combustion plays a decisive role. Flash point is an important parameter that indicates the evaporation characteristics of combustible liquids, which can be used to measure the evaporation characteristics of flammable and explosive volatile liquids and the size of the combustion hazard.
(2) spontaneous combustion flammable volatile liquids in the absence of an ignition source under the role of external heating caused by the ignition phenomenon known as spontaneous combustion fire. The spontaneous ignition point of the liquid is not a fixed parameter of physical properties, it is not only related to its nature, but also by the pressure, vapor concentration, oxygen content, catalyst, container characteristics and other factors. Flammable and explosive volatile liquids can ignite spontaneously when heated to the auto-ignition point, and the lower the auto-ignition point, the greater the fire hazard. Generally speaking, the auto-ignition point of homologue decreases with the increase of molecular weight, because the bond energy of chemical bond in homologue becomes smaller with the increase of molecular weight, thus the reaction rate is accelerated and the auto-ignition point decreases.
(3) flow diffusion of flammable and explosive volatile liquids, such as leakage, will be quickly dispersed in all directions. Because of the capillary effect and infiltration, can expand the surface area of flammable liquids, accelerate evaporation, increase its concentration in the air, easy to fire spread. In the fire, the liquid flowing along the terrain will form a “flowing fire”, the flow rate will often make the scene of trapped people and fire rescue personnel to retreat in time, resulting in major casualties.
(4) friction charged Most flammable and explosive volatile liquids are dielectrics, such as ether, ester, carbon disulfide resistivity are more than 10 3 Ω – cm, they are in the filling, conveying, jetting process is very easy to generate static charges, if no attention is paid to the above process of grounding in a timely manner will be charged to lead away, when static charges to a certain degree, it will discharge sparks, resulting in a flammable and volatile explosive liquid combustion and explosion.
2. Flammable and explosive volatile liquid explosion prevention
Measures to prevent fires and explosions of flammable and explosive volatile liquids are based on the following five techniques and principles: exclusion of the source of ignition; exclusion of air (oxygen); storage of liquids in closed containers or devices; ventilation to prevent the concentration of vapors of flammable and explosive volatile liquids from reaching the range of combustion concentrations; and substitution of air with inert gases. The last four methods are to prevent flammable volatile liquids (vapors) and air constitute a combustion, explosion mixture. These five methods are used at the same time, the specific practices are as follows:
(1) The production, use and storage of flammable and explosive volatile liquids in the plant and warehouse should be one or two level fire-resistant buildings, which should be well ventilated, strictly prohibit fire and smoke in the surrounding area, and be far away from fire, heat, oxidizing agents and acids. In summer, there should be thermal insulation and cooling measures, flash point lower than 23 ℃ flammable and explosive volatile liquids, the warehouse temperature is generally not more than 30 ℃; low boiling point species, such as ether, carbon disulfide, petroleum ether and other warehouses, it is desirable to take measures to reduce the temperature of refrigeration. Large quantities of storage of benzene, ethanol, gasoline, etc., generally available storage tanks. Storage tanks can be located in the open air, but the temperature above 30 ℃ should be used to force cooling measures.
(2) The use and storage of flammable and explosive volatile liquids should be based on the relevant regulations and standards to choose explosion-proof appliances. In the loading and unloading and handling should be light, prohibited rolling, friction, dragging and other operations that jeopardize safety. It is strictly prohibited to use spark-prone iron tools and wear shoes with iron nails during operation. Motor vehicles that must enter the premises should preferably be of explosion-proof type, and their exhaust pipes should be installed with reliable spark extinguishers and protective baffles or heat-insulating panels to prevent flammable materials from dripping on the exhaust pipes.
(3) When filling flammable and explosive volatile liquids, the container should be left with more than 5% empty space and should not be filled to the brim in order to prevent flammable and explosive volatile liquids from expanding or exploding due to heat.
(4) They shall not be mixed with other chemical hazards. Experimental and retained as a sample of a small number of bottles of flammable and explosive volatile liquids can be set up dangerous chemicals cabinet, according to the nature of the compartment storage, the same compartment shall not be stored in the nature of the conflicting items.
(5) For flammable and explosive volatile liquids of different natures and different degrees of danger, storage conditions should be selected in accordance with the regulations. In particular, for low flash point flammable and explosive volatile liquids, the storage conditions should be more stringent, if necessary, to take inert gas protection.
(6) In the whole process of production, transportation, loading and unloading, storage and use, take effective anti-static and lightning measures to prevent the occurrence of static fires and lightning fires.
Chapter III Prevention of dust explosions
In 1906, France, Couriers (Couriers) coal mine explosion, resulting in 1,099 deaths, shocking countries. This is when scholars began to pay real attention to the study of dust explosions, but the research field was limited to major coal mines. During the Second World War, the scope of research on dust explosions only gradually broadened to metal, chemical raw materials plants. Dust accidents have also occurred in recent years, on August 2, 2014, an aluminum dust explosion occurred in Suzhou Kunshan Zhongrong Machinery Factory; on April 29, 2016, an aluminum dust explosion occurred in Shenzhen Jingyixing Hardware Factory: on March 31, 2019, a deflagration accident occurred in a container storing magnesium alloy scrap waste outside the machining workshop of Suzhou Kunshan Hunding Precision Metals Co, Ltd, resulting in seven deaths and five people were injured. The occurrence of these accidents caused serious casualties and brought huge economic losses to society, and at the same time, it also sounded the alarm of dust explosion prevention and control, which aroused great concern in society.
1. Dust explosion conditions
Typically, five elements are required for a dust explosion:
(1) Combustible dust is present;
(2) Dust is suspended in the air at a certain concentration;
(3) The presence of an ignition source sufficient to cause a dust explosion;
(4) Auxiliaries;
(5) Limited space.
With the above conditions of the dust can explode, is due to the suspension of combustible dust in the air to form a highly dispersed system, its surface energy (embodied in the adsorption and activity) greatly increased: at the same time, dust particles and the air between the interface between the oxygen to increase the supply of oxygen is more than enough, a sufficiently energetic ignition source, the reaction rate increased sharply and was an explosive state.
2. The process and characteristics of the dust explosion
The vast majority of dust explosion to go through the following stages: first of all, suspended in the air combustible dust surface to accept the energy of the ignition source, the surface temperature rises rapidly; secondly, the surface of the dust particles of the molecular thermal decomposition or dry distillation, resulting in the release of combustible gases from the surface of the dust particles to the gas phase; and then, the release of combustible gases and air (or oxygen and other combustion-assisted gases) mixed with the formation of an explosive mixture. Subsequently ignited by the ignition source to produce a flame; finally, the heat propagated by this flame and further promote the decomposition of the surrounding dust, the continuous release of combustible gases in the gas phase, and mixed with the air, so that the flame continues to propagate, resulting in a violent dust explosion.
Compared with the general gas explosion, dust explosion has the following characteristics:
(1) multiple explosions is the most important feature of the dust explosion. The first explosion of the air wave will be deposited in the equipment or dust on the ground blowing up, in the short time after the explosion will form a negative pressure in the center of the explosion, the surrounding fresh air will be filled in from the outside to the inside, and the dust raised by mixing, thus triggering a secondary explosion. The second explosion, the dust concentration will be higher.
(2) The minimum ignition energy required for a dust explosion is generally in the order of tens of millijoules or more.
(3) dust explosion pressure rises slowly, the higher pressure lasts a long time, the release of energy, strong destructive force.
3. Prevention and control of dust explosions
Preventing dust explosion accidents, avoiding casualties in dust explosion accidents, and reducing losses in dust explosion accidents have all become common concerns of relevant industry practitioners and regulatory authorities. According to the five elements of dust explosion and related influencing factors, as long as in the production to destroy the formation of one or more of them, you can do to prevent dust explosions.
(1) Optimize the layout design When layout design is carried out for the plant, firstly, the location of the plant should be selected reasonably, and the location of the dust workshop on the general plan of the plant should be reasonable. For centralized heating areas, it should be located on the downwind side of the dominant wind direction in the non-heating season of other buildings In non-centralized heating areas, it should be located on the downwind side of the dominant wind direction throughout the year. Buildings (structures) installed with dust explosion hazardous process equipment or the presence of combustible dust should be separated from other buildings (structures), and their fire separation should be in accordance with relevant regulations. The building should be a single-story building, and the roof should be a light structure.
(2) control of dust aggregation, suspension and flying Timely elimination of combustible dust suspended in the air, reduce the concentration of combustible dust in the combustible material, to ensure that it is not within the explosion limit, to fundamentally prevent the occurrence of combustible dust explosion.
a. Reduce dust exposure. Technical means of effectively reducing dust exposure are through the enclosed operation of production equipment and the installation of dust-absorbing equipment for dust-producing points.
b. Dust suppression measures. Dust suppression measures are measures that inhibit the floating state of dust or reduce the amount of dust generated.
c. Eliminate positive pressure. Dust from the production equipment in the escape of one of the reasons for the material drop induced a large amount of air in the closed cover to form a positive pressure, in order to attenuate and eliminate this effect, should reduce the height difference between the falling material, properly reduce the chute tilt angle, isolation of the airflow, reduce the amount of induced air, reduce the lower part of the positive pressure and so on.
d. Enhanced dust removal. Enhanced dust removal refers to measures to reduce dust concentration through ventilation and dust removal systems, which can be used as a localized dust removal system or supplemented by full exhaust or natural exhaust. Ventilation and dust removal should be set up in accordance with the process of relatively independent dust removal system, all dust-producing points should be equipped with dust-absorbing hoods, there should be no dust precipitation in the duct, and the installation, use and maintenance of dust collectors should be in line with the relevant provisions. In addition, there are electrostatic dust elimination and wet dust elimination and other measures. Electrostatic dust elimination device is based on the electric dust removal and dust source control methods, which mainly includes high-voltage power supply equipment and electric dust collection device (including closed hoods and exhaust ducts) two parts. Wet dust elimination means that under the conditions allowed by the process, wet dust elimination measures can be used to achieve the purpose of dust prevention. In the aluminum and magnesium dust wet dust elimination process, the use of spiral spray nozzles solves the problem of the traditional nozzle easy to clog, and improves the efficiency of dust capture. In addition, for the current mining dust collector exists in the low efficiency, maintenance workload, scholars designed a PLC (programmable controller) automatic control of the flat bag dust removal system, improve the dust removal efficiency and system reliability.
e. Dust reduction measures. Dust abatement is mainly a measure that uses methods such as spraying to trap dust that has been generated and turned into a floating state.
f. Control the relative humidity of the air in the workplace. Reasonable and effective arrangement of humidification spraying device in the production workshop can increase the relative humidity of the air, thus reducing the dispersion of dust, improving the dust settling speed, and avoiding the dust to reach the explosion concentration limit. When the relative humidity of the air reaches 65% or more, it can effectively promote the settlement of dust and prevent the formation of dust clouds.
g. Other setup requirements such as floor and gutter. Non-sparking floor materials should be used, and if insulating materials are used as the overall surface, anti-static measures should be taken: the internal surface of the plant emitting combustible dust and fibers should be flat, smooth and easy to clean: it is not desirable to set up a gutter in the plant, and if it is necessary to do so, the cover should be tight, and effective measures should be taken to prevent combustible gases, flammable vapors and dust from accumulating in the gutter, and it should be connected with the neighboring plant. Sealed with fireproof material.
(3) Preventing dust clouds and dust layers from catching fire In preventing spontaneous combustion of powders, hot powders capable of spontaneous combustion should be cooled to the normal storage temperature before storage; when storing bulk powders capable of spontaneous combustion in large quantities, the temperature of the powders should be continuously monitored; when the temperature is found to be elevated or gases are precipitated, measures should be taken to cool down the powder; and the unloading system should be equipped with measures to prevent the aggregation of powders.
(4) Elimination of controlled sources of ignition Elimination of controlled sources of ignition is a key step in the prevention of dust explosions. Specific to a particular source of ignition, must be based on the specific operating environment for targeted prevention of ignition sources, here are some specific requirements and measures.
a. Preventing open flames and hot surfaces from igniting. The first step is to control man-made ignition sources and to prohibit all types of open flames, such as cigarettes, lighting, cutting, etc., in combustible dust sites. All combustible dust production areas should be classified as no-fire zones, and the use of open flames should be strictly controlled.
If it is necessary to carry out open-flame operation in the dust explosion hazardous place, the following provisions should be observed: approved by the person in charge of safety and obtain a fire permit; before the start of the open-flame operation, the combustible dust in the open-flame operation place should be cleared and equipped with sufficient fire extinguishing equipment; the section where the open-flame operation is carried out should be separated or partitioned from the other sections: during the period of the open-flame operation and during the cooling period after completion of the operation, there should not be any dust into the open-flame operation place. The work shall be separated or partitioned from other zones.
b. Protection against electric arcs and sparks. In dust explosion hazardous places, corresponding lightning protection measures should be taken. When there is a danger of static electricity, anti-static facilities should be installed at the site, and measures such as electrostatic grounding should be taken for pipes and equipment. All metal equipment, device shells, metal piping, brackets, components, parts, etc., generally use anti-static direct grounding, inconvenient direct grounding, can be indirectly grounded through the conductive materials or products; directly used to contain the apparatus for starting the powder, the pipeline for conveying powder (belt), etc., should be made of metal or anti-static materials, and all metal piping connections (such as flanges) should be spanned: the operator shall Operators should take anti-static measures. In accordance with the standard of “General Guidelines for Prevention of Static Electricity Accidents”, corresponding preventive measures should be taken for the selection of materials, equipment installation and antistatic design, operation and management of the process, so as to control the generation of static electricity and the gathering of electric charge.
(5) control of combustion-inducing substances The main preventive measure in this area is the use of inert gas protection. The principle of inert gas protection is in the mixture of dust and air, filled with inert gases that are neither flammable nor combustion-inducing, reducing the oxygen content in the system, so that dust explosions can not occur due to lack of oxygen. Inert gases such as CO2 and N2 are commonly used in industry to inert the workshop.
(6) space constraints The current mainstream method of solving the problem of space constraints is to set up explosion-proof pressure relief devices. Practical experience shows that in the appropriate parts of the equipment or plant to set up a weak surface (pressure relief surface), which can be discharged to the outside of the explosion of the initial pressure, flame, dust and products, thereby reducing the explosion pressure, reduce the explosion loss. The use of explosion relief technology, must pay close attention to the need to consider the maximum pressure of dust explosion and the maximum pressure rate, in addition to the volume and structure of the equipment or plant should be taken into account, as well as the pressure relief surface of the material, strength, shape and structure. Used as a pressure relief surface of the facilities are blasting plate, side door, hinged windows, etc.; pressure relief surface can be made of metal foil, waterproof paper, tarpaulin, plastic sheets, rubber, asbestos, gypsum board, etc..
(7) Other factors In general, dust explosions need to have five elements: combustible dust, dust cloud, ignition source, accelerants, space restrictions. In addition, the dust explosion there are several important factors affecting the following, the prevention of dust explosions is of great significance.
a. Dust explosion limit. Dust to a certain concentration suspended in the air is one of the conditions for the occurrence of a dust explosion, the “certain concentration” quantification is the dust explosion limit. Dust explosion limit is a mixture of dust and air can explode in case of ignition sources of dust minimum concentration (lower limit) or maximum concentration (upper limit), generally expressed in terms of unit volume of space contained in the dust mass. In the known composition of chemical dust and heat of combustion, and make certain simplifying assumptions, can calculate the explosion limit, but usually using specialized instruments to determine. Experiments have shown that many industrial dusts have a lower explosive limit of 20-60g/m³ and an upper explosive limit of 2000-6000g/m³.
b. Minimum detonation energy of the explosion. Dust explosion of the minimum detonation energy, can also be obtained from the spark discharge energy. Combustible dust touching the ignition source energy more than its minimum detonation energy, it can explode. Therefore, control the minimum detonation energy of dust in the prevention of dust explosion is of great significance.
c. Physical and chemical properties of dust. Containing more combustible volatile components of the dust, the greater the risk of explosion, and its explosion pressure and pressure rise rate is higher. Because this type of dust volatile release more gas, a large amount of gas and air mixed to form an explosive mixture, making the system reaction more easily and violently. As the heat of combustion and the dust release of the amount of gas has a relationship, so the high heat of combustion of the dust is prone to explosion; in addition, the oxidation rate of the dust such as magnesium, ferrous oxide, dyes, etc. are prone to explosion, and the maximum explosion pressure is larger, easy to charge the dust is also prone to explosion.
d. Particle size of dust. Particle size is an important influence on the dust explosion. The smaller the particle size of the dust, the larger the specific surface area, the greater the dispersion in the air and the longer the suspension time, the stronger the activity of adsorbed oxygen, the faster the rate of oxidation reaction, and therefore the more likely to explode, that is, the minimum ignition energy and the lower limit of the explosion is smaller, and the maximum explosion pressure and the maximum rate of pressure rise correspondingly larger. If the particle size of the dust is too large, it will therefore lose explosive properties. Such as particle size greater than 400μm polyethylene, flour and methylcellulose dust can not be explosive, and most coal dust particle size less than 1/15 ~ 1/10mm to have the ability to explode. Greater than the critical size of the explosion of coarse dust mixed with a certain amount of fine dust can be exploded, it may become an explosive mixture.