Automobile Factories Intelligent Lighting Solutions
Abstract:
High-quality lighting plays a crucial role in the modern automotive industry. For workers engaged in production or those in this industrial environment, the quality of lighting is of great significance to their working conditions, efficiency, and comfort.
In terms of functionality, the quality of lighting directly affects the quality of work for tasks completed through visual observation. Each process section in an automotive factory has its own lighting requirements, which are determined based on the owner’s rich design and production experience as well as relevant regulations. The application of the terms, the adoption of the most economical plan and the selection of various lighting parameters can achieve the goal of high efficiency and energy conservation while meeting the process requirements.
Key words: Automotive technology; Lighting standards; Lighting parameters; Factory
I. the importance of automotive factory lighting and general requirements High-quality lighting plays a vital role in the modern automotive industry.
For workers engaged in production or in this industrial environment, the quality of lighting is very important to their working status, efficiency and comfort. At the functional level, the quality of lighting directly affects the quality of work performed by visual observation. The improvement of industrial technology level is based on a lot of bloody production accidents, high quality and adapt to a variety of different production environment lighting equipment is constantly introduced. A number of efficient, good light distribution curve, longer life industrial lighting equipment came into being.
Each process segment of the automobile factory has its own lighting requirements, at the same time, each process link is generally linked like a chain, and the lighting environment has different requirements from the living environment and other production environments. Compared with traditional automobile factories, modern automobile production workshops also have higher comfort requirements for all aspects of the entire production environment due to their stricter quality control. It requires more modern process equipment, more efficient tools, more convenient logistics, a cleaner environment, more sound safety measures, and fresher air. Low noise and even soft music background environment, so corresponding to a high standard of production environment, more efficient, long life, light distribution curve more suitable lighting equipment has become a modern car factory must.
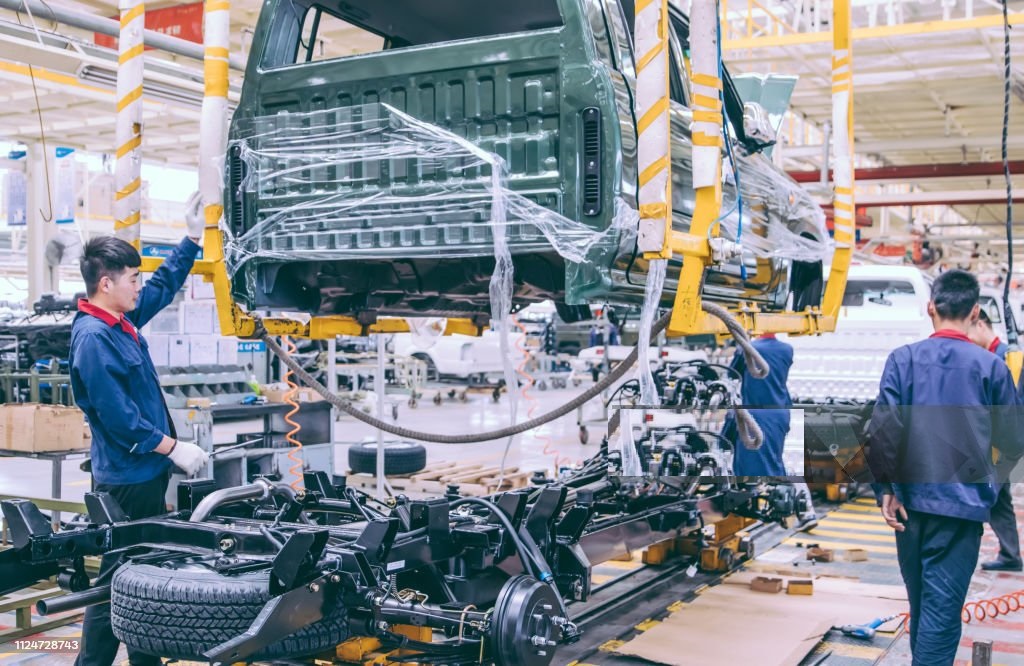
II. Brief Introduction to the Main Processes in Modern Automobile Factories
The main production processes in an automobile factory generally include four workshops: stamping workshop, body welding workshop, painting workshop, and final assembly workshop. The stamping process is the first step in all the procedures of a complete vehicle factory. In this process, steel plates are stamped into various components of the car body, such as the body shell, doors, roof, and chassis. Body welding is the process of joining the stamped steel plates of each component into a single unit, while ensuring that the car body has sufficient strength after being formed. Painting The main content of the process is anti-corrosion and painting, which is the most complex part of the process. It mainly includes surface treatment of the white body before painting and body painting, etc. The final assembly process is to install the engine, transmission, instrument panel, interior, seats, lights and other external components. The process of assembling purchased parts into the vehicle body to eventually form a fully functional car. Besides the “Four-person Process”, there are other auxiliary processes depending on the factory’s functions, which will not be elaborated here. III. Relevant Lighting Standards The first design standard for automotive factory lighting in our country is the “LED Lighting Design Standard for Automotive Industry Buildings” T/CIES023-2020 [1], which was developed by domestic lighting industry experts, industry design institutes, automotive manufacturers, and lighting equipment suppliers. This equipment manufacturer and several other parties jointly compiled it, which basically covers all the lighting environments in the automotive industry and also demonstrates a certain degree of advancement. It has significant guiding significance for the lighting design of automotive factories. It is also in line with the “Standard for Architectural Lighting Design” GB50034-2013 . It can fully provide data support for the lighting design of the car factory T.
In addition, some car manufacturers such as BMW, Volkswagen, and Tesla all have enterprise standards that make requirements for the lighting design of each process section. These requirements are based on the standards but exceed them. The main reason is that they have summarized the impact of lighting through years of production experience. The conclusion that the production accident rate decreases by approximately 40% when the actual illuminance is 7001x is based on years of production experience.
IV. Lighting Methods
According to the different visual requirements of various processes and areas in an automotive factory, choosing appropriate lighting methods and parameters can meet the process requirements while achieving the goal of energy conservation. Similar to many lighting facilities, automotive factory lighting is roughly divided into: For general lighting, local lighting and mixed lighting: General lighting, also known as overall lighting, is the lighting set up to illuminate the entire area; the purpose of local lighting is to supplement the lighting for areas with higher lighting requirements; mixed lighting refers to the combination of general lighting and local lighting. As the name suggests, it is a combination of the first two, and in some places it is also called combined lighting. For some areas with high requirements for the work surface and relatively small areas, relying solely on general lighting would result in significant waste or fail to meet the usage requirements. In such places where general lighting has already been installed, local lighting can be added to enhance the illumination of the work surface. The illuminance should be controlled to save energy. There are also relevant regulations on this in the lighting standards.
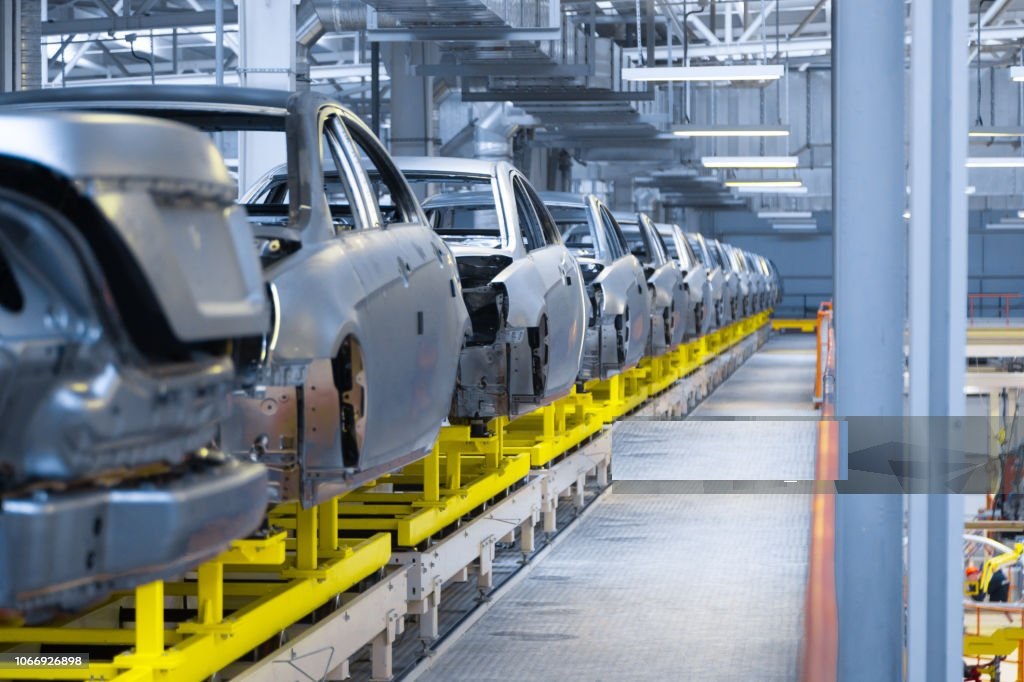
V. Key Parameters Involved in Lighting:
1. Lighting Standard Values: Different process sections have distinct operational characteristics, which determine varying lighting requirements. The core of this is the illuminance standard. According to the standard “Building Lighting Design Standard” GB50034-2013, it is stipulated that If the place has high requirements for precision or safety, such as fine operations, high-speed identification, difficult discrimination or significant safety responsibilities, the illuminance level can be raised by one grade. The deviation between the designed illuminance and the standard illuminance value should not exceed ±10%. Other The illuminance standards for production and supporting areas can all refer to the two national standards.
2. Maintenance Factor: The maintenance factor refers to the ratio of the average illuminance or average luminance on a specified surface after a certain period of use of the lighting fixture to the average illuminance or average luminance obtained on the same surface when the fixture was newly installed under the same conditions. Influences The factors influencing the maintenance coefficient mainly include the luminous flux maintenance rate of the light source, the residual rate of the light source, and the contamination of the luminaire, etc. The calculation method is not elaborated here.
3. Uniformity Illumination uniformity is an important indicator for enhancing visual satisfaction and reducing eye fatigue. It is defined as the ratio of the minimum illuminance to the average illuminance on the specified illuminated surface, that is, Emin/Eav. An effective way to improve illumination uniformity is to correctly select and install luminaires. When choosing the light distribution of lamps, for the general lighting of most standard factories, it is the simplest and most effective choice to appropriately select wide light distribution. If the factory is very high and has large equipment, such as a stamping workshop, narrow light distribution should be selected to achieve better uniformity of illuminance.
4. Color Temperature: The selection of the color temperature of the light source affects the psychological feelings of personnel in the workplace. It depends on many factors such as illuminance, the colors of the interior and equipment, climate conditions, and job requirements. Generally, we can choose the appropriate one according to the following chart. Correlation between color temperature and illuminance.
5. Color Rendering: According to the “Standard for LED Lighting Design in Automobile Industry Buildings”, for general lighting in large spaces with an installation height greater than 8m, the color rendering index of 1FD lamps should not be lower than 60. When used for general lighting in places where color discrimination is required, the color rendering index should be: It should not be lower than 80. When used for local lighting for color inspection, the color rendering index should not be lower than 90.
6. Glare Control: A visual phenomenon that causes discomfort or reduces the ability to observe details or targets due to an unsuitable distribution or range of brightness in the field of vision or the presence of extreme brightness contrast. In the automotive industry production environment, especially there Some visually demanding tasks, if there is a highly direct light source in the worker’s field of vision, will at best reduce production efficiency and at worst cause operational errors, leading to frequent accidents.
7. Unified Glare Rating (UGR) for indoor lighting glare assessment. The coughing light value, LGR value, caused by quasi-indoor space can be calculated based on the light distribution of the lamps under the conditions stipulated by TFC. The lighting design can select lamps accordingly and use it as a reference basis for the IGR value of indoor space. 8. Energy-saving Requirements: The energy-saving aspect of lighting is mainly reflected in the lighting power density (LPD). It refers to the installed lighting power per unit area (including light sources, ballasts or transformers), measured in watts per square meter (W/m²): “Design Standard for LED Lighting in Automotive Industry Buildings” Both the “T/C1ES023-2020” and the “Code for Design of Building Lighting” (GB50034-2013) have requirements for LPD.
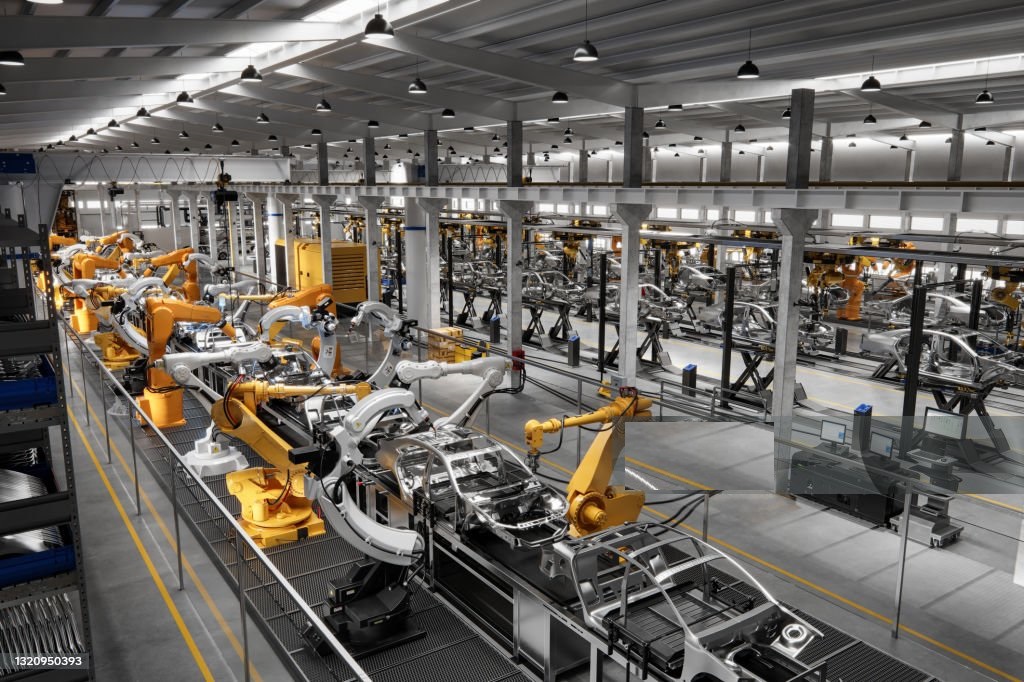
VI. Characteristics of Automobile Production Processes and Lighting Requirements:
Automobile production is an extremely complex process, from body stamping to body welding, paint spraying, power assembly, all the way to final assembly. It requires large-scale workshops, various types of mechanical equipment, instruments and meters, as well as the coordinated cooperation of different types of workers. Only in this way can it be accomplished. The rapidly developing automotive manufacturing industry encompasses a wide range of different working environments: from workshops to large factories, from precision work to heavy industrial production. In the practical application of lighting, due to the differences in venues, environments, job types, and so on, there are different requirements. The requirements for lighting also vary. Some well-known suppliers can already tailor lighting solutions for automotive manufacturers based on different needs, adapting to various working environments and supporting complex production processes, truly achieving safe production and increased efficiency. Efficiency and energy conservation.
1. Stamping workshop:
Process characteristics: Stamping is a crucial step in the body forming process. The assembly and transportation of large-tonnage stamping equipment and molds for this process need to be carried out by cranes lifting them in the air. Therefore, the height of the workshop is a key factor for the stamping workshop. One important feature is that, in line with the requirements of modern body forming, its spatial height often exceeds 15 meters and can even reach nearly 24 meters. Additionally, due to their large volume, stamping machines generate considerable noise and certain vibrations during the production process. Stamping equipment The foundation pit often requires maintenance. As it is located beneath the press, the environment is not only hot but also contaminated with oil.
Lighting equipment requirements:
Considering the high ceiling of the stamping workshop and to meet the environmental illuminance requirement of 3001x as stipulated, it is ideal to use high ceiling industrial lamps, which can ensure uniform and high lighting throughout the large space. Some important equipment requires Local lighting should be set up to provide the illuminance required for the detection and safety guarantee of the stamping process. The color temperature of the local lighting should be consistent with that of the general lighting, and the illuminance should meet the requirements of relevant standards. The layout of the lamps should take into account the positions of the press and other equipment to avoid the formation of shadow areas. The working illuminance should be enhanced. Meanwhile, for safety reasons, the lighting fixtures in the production area of the stamping workshop must be shockproof (such as IK08), and the lighting fixtures in the stamping pit should be oil-resistant and shockproof (such as IP65/IK08).
Due to the high ceiling of the stamping workshop, high ceiling LED fixtures (IP65/IK08) with narrow light distribution curves can be selected for general lighting, and they should be installed at small intervals to ensure an appropriate and uniform illumination level throughout the space. To ensure that the deep interior of the vehicle body can be illuminated, local lighting should be provided. The lighting fixtures can choose LED three-proof brackets (IP65/IK08) for local lighting. The color temperature should be consistent with that of general lighting. As the installation height of the fixtures is relatively low, impact-resistant fixtures are recommended. Smart dimming and zonal illuminance control can be adopted. In the main working areas of the stamping workshop (such as The production area, packing area, rework area, and mold maintenance/cleaning area shall follow the 300 lux illuminance standard, while other areas such as the pit area and logistics area shall follow the 150 lux illuminance standard. General lighting can be set up with working lighting and duty lighting (with an illuminance of 10% of the working lighting).
2. Body Welding Workshop:
After the various body components are formed through stamping processes, they are sent to the welding line in the welding workshop for welding. This workshop is responsible for welding the stamped parts together and is widely used in the manufacturing industry. Automation and flexibility in welding assembly. The degree determines the development prospects and future of welding. In automotive manufacturing, the welding core workshop includes welding pliers, welding machines, and conveyor lines, etc. The car body is a structural component made of thin plates. The sheet metal formed by stamping is assembled and welded to form the car body shell, also known as the white body. The body of a vehicle, therefore, welding assembly is the key to the shaping of the body and a major part of the automotive manufacturing process.
Welding production involves large batches, high production speeds, and high requirements for the assembly and welding accuracy of the parts to be welded. It mostly adopts a flow production method, with a high degree of mechanization and automation, and extensively uses specialized equipment and tooling fixtures. More and more welding work is being carried out by robots. The welding is accomplished by using arc welders and welding robots. During the welding process, certain smoke and dust are produced, making the environment dirty. The surface of the vehicle body materials turns gray, reducing visibility. Meanwhile, the completion of each component is carried out in different areas, so the entire operation is… The workshop appears rather dim. Welding! As there are no tall equipment in the welding workshop, the height of the factory building is generally not high, and the height of the beam bottom is mostly below 9 meters.
Lighting equipment requirements:
Since the bodies in the welding process are all gray, and the welding equipment will produce smoke when working, the welding production line needs to increase the illuminance to meet the requirements of brightness and uniformity in this section. The material of the lighting fixtures should be selected In sections with a lot of welding fumes and slag, closed-type lamps with easy-to-clean surfaces should be used.
For general lighting in the welding workshop, high-ceiling LED lamps with wide distribution and uniform arrangement can be selected. Linear LED track light strips can also be used, installed continuously, with distribution preventing reflective glare from bright metal surfaces or paint finishes, thus avoiding disruption of vision. For the welding base, Sections such as the dashboard, interior, and door trim typically require work station auxiliary lighting, i.e., local lighting. The inspection lighting in local areas needs to have high color rendering and be equipped with trace boards to avoid glare. Intelligent dimming or zoned illuminance control can be adopted. The inspection area in the welding workshop can follow the 1000 lux illuminance standard, while the three-coordinate room, measurement room, etc. can follow the 750 lux standard. Manual welding and assembly workstations should have 500 lux, and automatic welding and assembly workstations should have 200 lux. Other areas such as the logistics zone should follow the 150 lux illuminance standard. To facilitate energy conservation, Yes, general lighting can be set up with working lighting and duty lighting. The illuminance of duty lighting can be taken as 10% of that of working lighting. Refer to the lighting standard for illuminance, color temperature and illuminance uniformity.
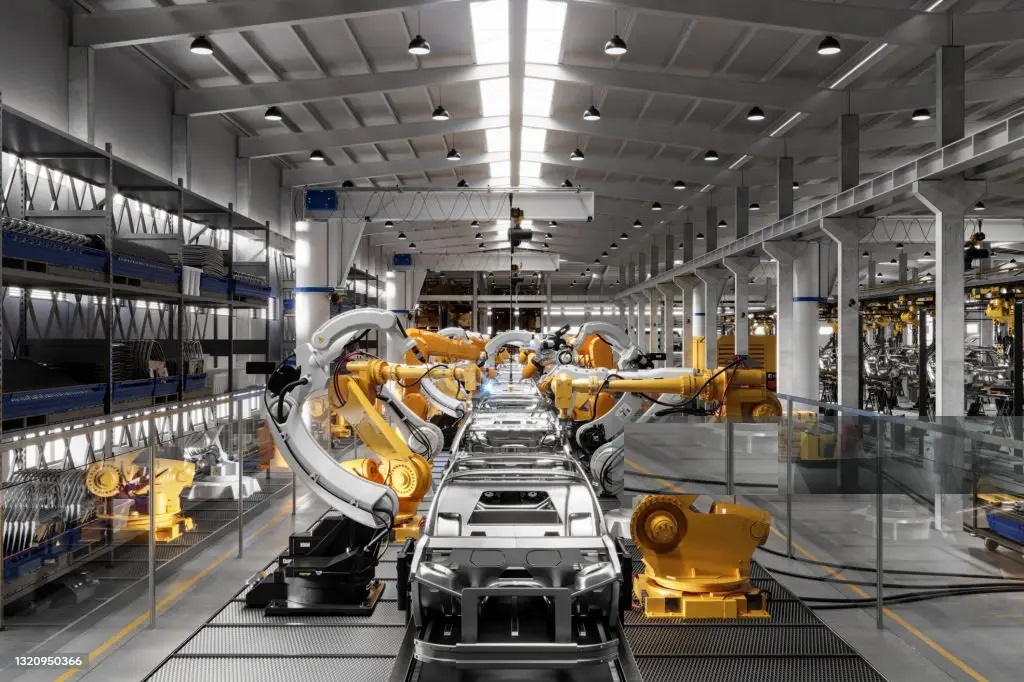
3. Painting workshop:
The nuclear light control color rendering painting process includes a cleaning and pre-painting line, a primer line and a sealing line (where the car body meets the water seal requirements through a lifting sealing line), and is a continuous automated operation. Workers monitor the entire process in a monitoring room. There are also some work in the work including spray gun painting, sandpaper grinding and other body repair and paint inspection work, the visual requirements are very high. The parts that have been sprayed will inevitably have bubble concealer on the surface, so quality inspection needs to be carried out after the spraying process. In the detection area, workers must be inspected quickly and effectively to ensure that the first time to find uneven surface, scratches, protrusions and other small defects, this process of human vision requirements are very high.
Lighting to ensure that quality inspection personnel timely find the body after painting defects, scratches, dirt and other defects. Horizontal and vertical rows of white diffused LED light sources produce a clean zebra-like stripe of light and dark to check for defects reflected on the body surface. Because only when the brightness of the projected surface is as high as possible, can better uniformity be obtained, so on the horizontal and vertical and related bevel, the surface illumination is required to be high and the uniformity is good. Good color rendering facilitates early detection of production defects. To reduce the possibility of glare, use optical processes or white screens for optimal viewing.
Lighting equipment requirements:
The coating detection process generally uses special lamps for paint inspection, LED lamps with high color rendering, especially zebra-print lamps, should be installed at a reasonable interval, and uniformity, illuminance and other tests should be carried out after installation. After years of application testing, this lighting setup can map the square light pulse wheel with clear edges on the paint of the car body, so that it can effectively detect small defects in the paint. In addition, spot lights are arranged on the roof and hood of the car. The narrow beam of the spotlight can simulate daylight and detect holograms created by polishing defects. The side of the vehicle is also illuminated by these spotlights for hologram inspection and subsequent maintenance, intelligent dimming/dividing illuminance/adjustable color temperature control in order to facilitate energy saving, general lighting can be set working lighting and on-duty lighting, on-duty lighting illumination can be 10% of the illumination of working lighting. The illumination of the inspection area of the painting workshop requires 15001x, the sanding and manual spray painter 10001x, the automatic spray painting section 5001x, the paint mixing room 3001x, other production areas 2001x, and the logistics area 1501x.
4. Final assembly workshop:
Final assembly is the process of assembling the parts purchased from the outside, such as the engine, gearbox, instrument, interior, seat and lamp, into the painted body and finally forming a fully functional car. On the assembly line, all internal and external accessories need to be installed on the car body. Automobile final assembly process can be roughly divided into the conveyor chain and platform assembly, these assembly process segments, the main work needs to rely on manual completion, sufficient illumination is the basic condition of production and security guarantee.
Lighting equipment requirements:
In addition to the general lighting in the installation workshop, the assembly section is set up local lighting equipment at a height of about 2.5 meters to supplement the general lighting with high illumination, while considering the use of asymmetric lamps, and the transmission line assembly is recommended to use continuous light belts. Because its lighting effect is better than the ordinary interval light strip. In the platform assembly unit, local lighting is generally installed, and ordinary factory lamps with high illumination can be used. In order to ensure that it can illuminate the interior of the car body, the installation height of the station lighting fixture is usually low, and at the same time, it is avoided Avoid possible collision hazards, it is recommended to use anti-collision, asymmetric lamps. In addition, the illumination requirement of the vertical plane of the assembly area will be higher than that of the horizontal plane, so it is recommended to use lamps with wide light distribution or towers of airfoil light distribution. For the Liding energy saving, general lighting can Set work lighting and duty lighting, duty lighting illumination can be 10% of work lighting illumination assembly station line, quality inspection/repair to implement 1000lux illumination standard, quality inspection room to implement 500lux illumination standard, assembly line general lighting 2001ux, other such as logistics area to implement 1501ux illumination standard.
In addition to stamping, body welding, painting, final assembly process, modern automobile factories according to their production and storage, testing requirements are different, there will be some auxiliary function of the process workshop, such as resin workshop, wax injection workshop, testing workshop, repair workshop, quality assurance workshop, submission workshop, etc. Although the name of these auxiliary workshops is different, but the function may be overlapping. The lighting requirements of each of their white can also be designed according to the two specifications and the principle of functional similarity with reference to the four major artistic lighting and local lighting requirements, which are not described here.
Germany, the United States, Japan, France, Korea and other mainstream countries of the automobile factory production process are not the same in all aspects, the lighting requirements are also “different from person to person”, although the requirements are different, but the completion of the ten process, staff safety protection, improve work efficiency, energy saving purposes are caused, we need to continue to accumulate experience, To improve the lighting design for different links.