Key Applications of 40W Flame Proof Lights in Rubber Factories: Safe and Efficient Industrial Lighting Solutions
Detailed Content (SEO-Optimized Keywords: 40W Flame Proof Light, Rubber Factory Safety Lighting, Industrial Flame Proof Solutions)
1. Unique Lighting Requirements of Rubber Factory Environments
Volatile Gas Risks
During rubber production, processes like mixing and vulcanization release flammable gases (e.g., solvent vapors, sulfides). Standard lighting fixtures may spark explosions. Flame proof lights must meet Ex d/IIC T4 standards, using flameproof enclosures to isolate internal arcs from external hazardous environments.
Dust and High-Temperature Challenges
High dust concentrations (e.g., carbon black particles) in mixing areas demand fixtures with IP65/IP66 ratings to prevent ingress. Vulcanization zones often exceed 80°C, requiring housings made of heat-resistant materials (e.g., aluminum alloy + tempered glass) to maintain seal integrity.
Corrosion Resistance Needs
Rubber additives (e.g., sulfur, chlorides) corrode metal components. Opt for anodized aluminum or 316 stainless steel housings to extend lifespan beyond 10 years.
2. Core Technical Advantages of 40W Flame Proof Lights
Flame Proof Design
Features flameproof enclosures + increased safety circuits, compliant with ATEX/IECEx certifications. Housing thickness ≥3mm with IK08 impact resistance ensures durability against mechanical and chemical damage.
Energy Efficiency and Longevity
LED modules deliver 2,000+ lumens, consuming 60% less energy than traditional 250W metal halide lamps. Constant-current drivers stabilize output under voltage fluctuations, achieving 50,000+ hours lifespan and reducing maintenance.
Installation Flexibility
Supports ceiling, wall, or embedded mounting. Example: Use 120° wide-angle floodlights in mixing areas and dimmable models (20-40W) in storage zones for adaptive coverage.
3. Lighting Layouts for Critical Rubber Factory Zones
Mixing Rooms
High dust zones require 40W flame proof floodlights (IP66) with 8-meter coverage radius to ensure ≥300 Lux illumination. Case study: A Southeast Asian factory reduced downtime by 90% post-upgrade.
Vulcanization Areas
In high-heat environments (60–100°C), select high-temperature-resistant models with ceramic substrates and heat-dissipation fins to maintain housing temperatures <80°C.
Storage Zones
Deploy dimmable lights (100–200 Lux) with motion sensors to cut energy use by 15% during idle periods.
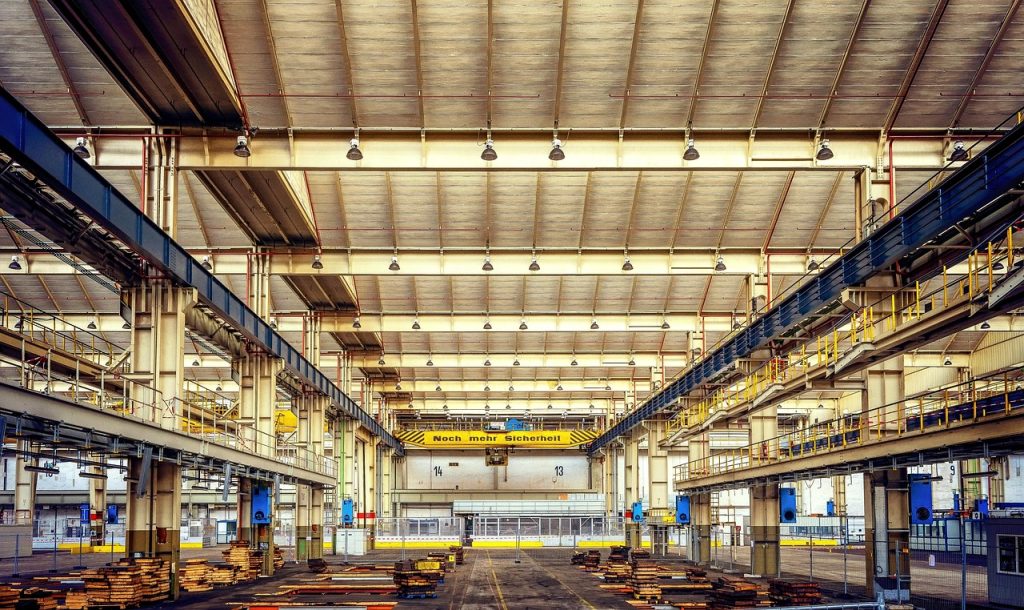
4. Role of Flame Proof Lights in Accident Prevention
Leak Detection Support
High color rendering (CRI >80) enhances visibility for spotting oil leaks or material defects. Example: A Thai factory reduced accidents by 40% after upgrading.
Emergency Lighting Integration
Built-in lithium batteries provide 30-minute backup lighting (≥10 Lux on escape routes). Linked to smoke sensors, they trigger alarms for faster evacuation.
Smart Sensor Capabilities
Connected via LoRa networks, lights auto-adjust brightness or activate ventilation when methane levels exceed thresholds, mitigating explosion risks.
5. Cost Savings and ROI Analysis
Energy Consumption Comparison
A 40W LED fixture uses ~200 kWh/year vs. 1,200 kWh for 250W metal halide lamps, saving **80/yearperunit∗∗(at0.10/kWh).
Maintenance Cost Reduction
Modular designs enable quick part replacements, slashing repair time by 70%. Case study: 5-year costs dropped 55% post-installation.
Insurance Premium Reductions
ATEX-certified lighting can lower factory insurance rates by 10–15% due to improved safety ratings.
6. Global Certifications and Compliance
ATEX & IECEx Dual Certifications
Ensures global compliance (EU, North America, Southeast Asia). The Ex db IIC T4 Gb mark confirms suitability for gases with ignition points ≥135°C.
Local Certification Adaptations
China’s GB3836 requires flameproof joint gaps ≤0.15mm, while Russia’s CU-TR mandates -40°C low-temperature testing.
Symbol Decoding
“Ex d” = flameproof, “IIC” = gas classification, “Gb” = equipment protection level. Match these to factory hazard zones (Zone 1/Zone 2).
7. Case Study: Southeast Asian Rubber Factory Retrofit
Project Background
A Thai plant reduced annual fixture failures from 12 to 1 after installing 200x 40W flame proof lights, cutting maintenance costs by 85%.
Technical Solution
Zoned deployment: 80x floodlights (mixing), 50x high-temperature models (vulcanization), 70x dimmable lights (storage). Smart dimming saved 30% energy.
Long-Term ROI
Achieved 220% ROI in 3 years, earning Thailand’s “Best Safety Practice Award” and boosting new orders by 25%.
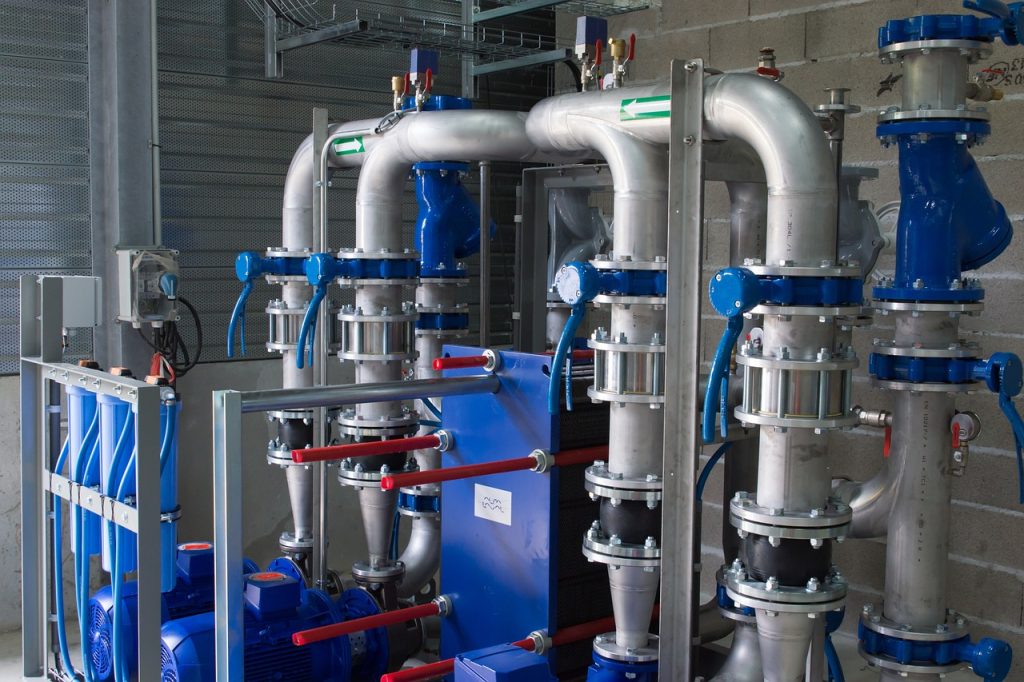
8. Supplier Selection and Procurement Tips
Certification Verification
Require third-party reports (e.g., SGS, TÜV) and confirm ISO 9001 compliance.
Customization Capabilities
Ensure suppliers offer material (316 stainless steel/aluminum) and optical customization (spot/flood lenses). Example: A Vietnamese client extended product life by 3 years with anti-corrosion coatings.
After-Sales Support
Demand ≥5-year warranties and 24/7 local technical support. Case: A Malaysian client received replacements within 48 hours after flood damage.
FAQ: Common Questions About 40W Flame Proof Lights in Rubber Factories
Q1: Can 40W flame proof lights cover large rubber factory areas?
A: Yes. With 2,000+ lumens and 120° lenses, each light covers 8–10m radius. Proper spacing (6–8m) ensures ≥300 Lux in mixing rooms.
Q2: Does high dust affect fixture lifespan?
A: No. IP66 sealing blocks dust ingress. Anti-static coatings prevent particle buildup. Real-world tests show ≤5% light depreciation after 3 years.
Q3: Why choose ATEX/IECEx-certified lights?
A: Compliance reduces legal risks and insurance costs by 10–15%. Non-certified products may trigger explosions or penalties.
Q4: Do lights fail in vulcanization heat?
A: High-temperature models use ceramic substrates and heat sinks to maintain housing temps <80°C. Proven in 90°C environments for 5+ years.
Q5: How to calculate energy savings?
A: A 40W LED saves ~120/yearvs.250Wmetalhalide(at0.12/kWh). Fewer replacements cut long-term costs by 55%.
Q6: Are smart controls supported?
A: Yes. Integrate via LoRa/ZigBee for remote dimming, fault alerts, and energy tracking. A Malaysian plant reduced maintenance costs by 35%.
Q7: Do installations require rewiring?
A: No. Fixtures support 100–277V input and retrofit existing setups. Ensure proper grounding (resistance ≤4Ω).
Q8: How to verify corrosion resistance?
A: Check material specs (e.g., 316 stainless steel) and request salt spray test reports (≥1,000 hours).