How to Distinguish Explosion-Proof Cable Glands from Standard Ones? Key Differences and Selection Guide
Explosion-proof cable glands and standard cable glands are essential components for cable sealing in industrial equipment, but their designs, functions, and applications differ significantly. This article breaks down their material composition, certifications, pricing, and use cases, and provides a specification selection guide for explosion-proof cable glands to help users make informed decisions.
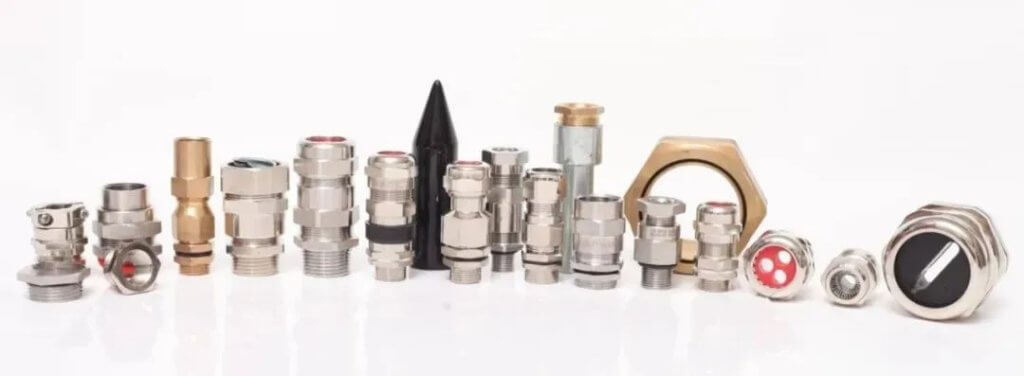
1. 4 Key Differences Between Explosion-Proof and Standard Cable Glands
1. Material: Metal vs. Plastic
- Explosion-Proof Glands: Made of high-strength metals like 304/316 stainless steel, brass, or carbon steel, these resist corrosion, high temperatures, and mechanical stress. Their metal construction isolates internal sparks from flammable external environments.
- Standard Glands: Typically use engineering plastics (e.g., nylon, PVC). While cost-effective, they degrade quickly in harsh or corrosive conditions.
2. Certifications: Explosion-Proof Compliance vs. Basic Standards
- Explosion-Proof Glands: Require national certifications (e.g., China’s Ex, ATEX, or IECEx) and include explosion-proof test reports and 3C certificates. Products are marked with an “Ex” symbol, indicating compliance with GB3836 or similar standards.
- Standard Glands: Only need basic IP66/IP67 ratings for water/dust resistance, with no explosion-proof certifications.
3. Pricing: Premium Safety vs. Budget Solutions
- Explosion-Proof Glands: Cost 3–5× more than standard glands due to materials and certifications. For example, stainless steel variants range from 3–3–15 USD, while specialized models cost higher.
- Standard Glands: Priced between 0.5–0.5–3 USD, ideal for non-hazardous environments.
4. Applications: Hazardous Zones vs. General Use
- Explosion-Proof Glands: Designed for oil/gas refineries, chemical plants, mines, and pharmaceutical facilities with explosive gases/dust. Used in explosion-proof control boxes, lighting, and instruments for fire/explosion prevention, corrosion resistance, and IP68 sealing.
- Standard Glands: Suit general electrical cabinets, control panels, and outdoor lighting requiring basic water/dust protection.
2. Explosion-Proof Cable Gland Sizing Guide
1. Core Specifications Comparison
Parameter | Armored Type | Non-Armored Type |
---|---|---|
Cable Type | Metal-armored cables | Rubber/plastic sheathed cables |
Sealing | Dual-layer (rubber + lock) | Single rubber seal |
Thread Type | G (parallel), NPT (tapered), M (metric) | Same as left |
IP Rating | IP68 (submersible) | IP67 (temporary immersion) |
2. Common Sizes & Use Cases
- Thread Sizes: M16×1.5, M20×1.5, G1/2, NPT1/2, etc.
- Cable Diameter: Φ5–Φ80mm, compatible with single/multi-core cables.
- Selection Tips:
- Chemical Plants: Opt for 316 stainless steel + NPT threads for acid resistance.
- Mining: Use Ex d-certified glands with G threads.
- Marine Environments: Choose armored dual-seal glands with IP68.

3. How to Identify Explosion-Proof Cable Glands?
- Check Markings: Look for “Ex” labels and explosion-proof ratings (e.g., Ex IIB T4).
- Material Test: Use a magnet—stainless steel (non-magnetic) and brass differ from plastic.
- Verify Certificates: Request Ex compliance documents and validate certification IDs.
4. Specialized Application Recommendations
- High Temperatures: Choose nickel-plated brass or 316L stainless steel (withstands 400°C).
- Corrosive Areas: Use PTFE seals + stainless steel bodies for chemical resistance.
- Vibration-Prone Zones: Select armored glands with spring-loaded locking to prevent cable loosening.
Συμπέρασμα
Choosing the correct explosion-proof cable gland is critical for safety in hazardous environments. By evaluating materials, certifications, and application needs alongside technical specifications, users can maximize protection. Always source from ISO 9001-certified suppliers and routinely inspect seals for wear. Prioritize quality to ensure long-term reliability and compliance.