Explosion Protection in Petrochemical Processes: Core Risks & Safety Control Technologies
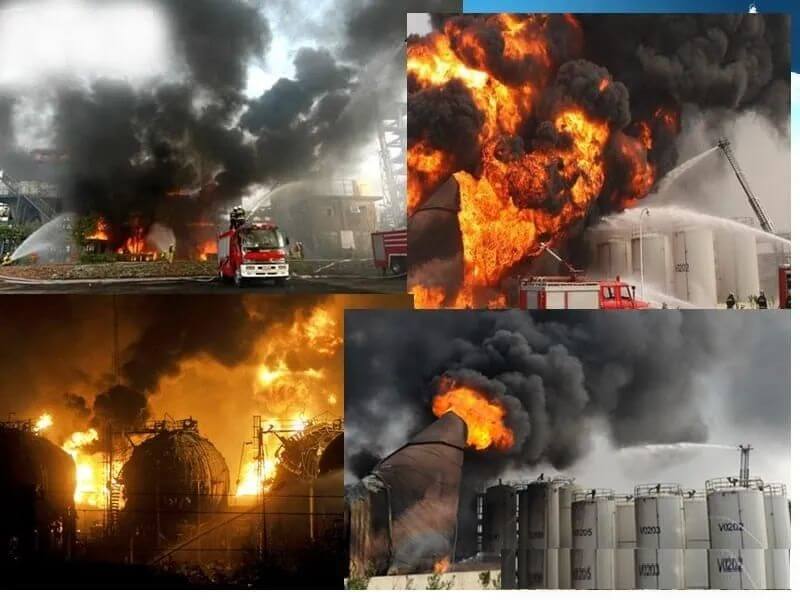
I. Unique Explosion Risks in Petrochemical Industry
Petrochemical operations face elevated explosion risks due to:
- Multiple ignition sources: 90%+ raw materials are flammable (flash points <23℃), 68% incidents involve static electricity
- Equipment vulnerabilities: 80% pressure vessels show stress corrosion, 45% facilities exceed 10-year service life
- Process complexity: 72% chain reactions occur within 8 seconds in continuous systems
- Mega-scale impacts: Explosions in 10M-ton refineries can cause $1B+ losses
II. Critical Process Safety Controls
1. Oxidation Reaction Safety
Key hazards:
- Autoignition temperatures: Methanol (464℃), Acetaldehyde (185℃)
- Peroxide formation risk: Acetic peroxide decomposition at 110℃
Prevention measures:
- Triple-redundant temperature control (±1.5℃ accuracy)
- Dual-layer flame arrestors (velocity >500m/s)
- Real-time peroxide monitoring (PID detectors)
2. Hydrogenation Process Safety
Explosion prevention:
- Nickel catalyst activation: O₂ <0.5% via nitrogen purge
- Hydrogen detection: Catalytic bead sensors (0-100% LEL range)
- Microreactor technology: 95% reduction in H₂ inventory
Chemical handling:
- NaBH₄ storage: <30% RH humidity control
- Na₂S₂O₄ dissolution: <25℃ with jacketed mixers
3. Electrolysis Safety Standards
Chlor-alkali critical parameters:
Parameter | Standard | Risk Threshold |
---|---|---|
H₂ in Cl₂ | <2.0% per cell | >5% explosion |
NH₄⁺ in brine | <0.3ppm | NCl₃ formation |
Amalgam temp | 93±1℃ | Na accumulation |
Innovations:
- Membrane cell technology (zero mercury)
- UPS + diesel backup (200ms switch time)
4. Polymerization Risk Management
Accident patterns:
- Ethylene runaway reactions (>300℃)
- VCM polymerization stirrer failure
Advanced controls:
- Distributed Control Systems (DCS)
- Supercritical CO₂ expansion tech
- Emergency kill systems (response <2s)
5. FCC Unit Protection
Key safeguards:
- Regenerator-Reactor ΔP control (±3kPa)
- Catalyst circulation monitoring (γ-ray densitometers)
- CO boiler safeguards (O₂ trim control)
Equipment integrity:
- Redundant air blowers (5s failover)
- Third-stage separators (99.99% efficiency)
- Acoustic emission testing (ASTM E1106)
6. Nitration/Chlorination Safety
Nitration controls:
- Mixed acid temp gradient <75℃
- Continuous flow reactors (residence <15s)
- Effluent neutralization (pH 6.5-7.5)
Chlorination innovations:
- UV-initiated reactions (T reduction 150℃)
- AI-based Cl₂ leak detection (0.2s response)
- Double mechanical seals + bellows
III. Explosion Protection in Petrochemical: Next-Gen Explosion Prevention Tech
- IIoT Predictive Maintenance: Vibration + thermal imaging
- Inherent Safety Design: Modular microreactors
- Digital Twin Systems: HAZOP dynamic simulation
- Advanced Materials: Graphene-enhanced flame arrestors
Key Standards:
- API RP 752 (Process Unit Siting)
- NFPA 69 (Explosion Prevention Systems)
- EN 1127-1:2019 (Explosive Atmospheres)
Expert Tip: Implement SIL 3 safety loops for critical processes and conduct quarterly LOPA studies.
Adopting these measures can reduce explosion incidents by 65%+ based on AIChE PSID data. Recommended annual safety investment: 2.5-3.5% of CAPEX.