Zone 1 vs Division 1: How Explosion Proof and Flame Proof Labels Impact Industrial Lighting Selection
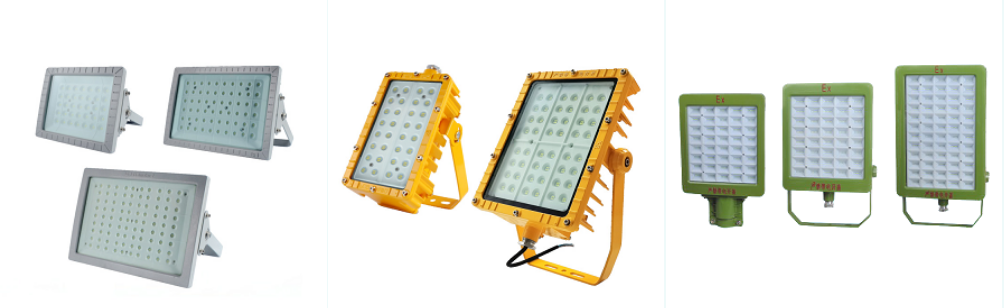
Navigating Global Standards for Hazardous Area Compliance
Introduction: The Critical Role of Classification Systems
Industrial facilities operating in hazardous environments—such as oil refineries, chemical plants, and mining operations—rely on precise classification systems to mitigate explosion risks.
The terms Zone 1 (IEC/ATEX) and Division 1 (NEC) define distinct approaches to classifying explosive atmospheres, directly influencing the selection of explosion-proof (Ex d) and flame-proof lighting solutions.
This article decodes these standards, their material requirements, and their practical implications for industrial lighting design
1. Zone 1 vs Division 1: Core Differences in Hazard Classification
A. Zone 1 (IEC/ATEX Standards)
Definition: Zone 1 designates areas where explosive gas atmospheres are likely to occur occasionally during normal operations (e.g., during maintenance or leaks).
Certification Focus: ATEX/IECEx emphasizes explosion containment, requiring enclosures to withstand internal blasts without igniting external atmospheres.
Material Requirements: Aluminum or stainless steel housings with flame paths ≤0.05mm gaps, tested to EN 60079-1 for pressure resistance (≥1.5x explosive force).
B. Division 1 (NEC 500/505)
Definition: Division 1 applies to environments where hazardous gases, vapors, or dusts are present continuously or frequently under normal conditions.
Certification Focus: UL 844 prioritizes flame resistance, ensuring external surfaces resist ignition from nearby fires.
Material Requirements: Flame-retardant polycarbonate lenses and epoxy-sealed joints to prevent flame penetration.
Key Contrast:
Risk Duration: Zone 1 addresses intermittent hazards, while Division 1 targets persistent risks.
Testing Protocols: Zone 1 fixtures undergo cyclic explosion tests (5+ pressure cycles), whereas Division 1 lights focus on continuous flame exposure.
2. Certification Challenges: Regional Standards and Material Innovations
A. ATEX vs NEC Compliance
Europe (ATEX): Mandates dual certification for combined gas/dust hazards (e.g., Zone 1/21). Example: QLEX-SLM-250-ATEX light bars use polycarbonate lenses and aluminum housings to meet Ex d IIC T6 ratings.
North America (NEC): Division 1 lights often lack dust ignition protection (NFPA 70), requiring supplemental IP6X sealing for grain silos or pharmaceutical facilities.
B. Hybrid Solutions for Global Markets
Case Study: Offshore oil platforms demand ATEX Zone 1 + NEC Division 1 compliance. Solutions include triple-sealed LED modules with ceramic flame arrestors, reducing maintenance costs by 30% in saltwater environments.
Material Breakthroughs:
Conductive Epoxy Gaskets: Prevent static sparks in methane-rich Division 1 coal mines.
Nano-Ceramic Coatings: Enhance flame resistance on aluminum housings, tested to 800°C for LNG storage zones.
3. Application-Specific Lighting Strategies
A. Oil & Gas Facilities
Zone 1: Use explosion-proof LED floodlights with pressure-relief valves (e.g., GUANMN’s Ex d-rated fixtures for refinery pipe racks).
Division 1: Deploy flame-proof halogen backups with <85°C surface temperatures to prevent igniting hydrogen sulfide.
B. Chemical Processing Plants
Dual Certification: Combustible dust (Zone 21) and vapors (Division 1) require fixtures with IP65 sealing and Ex tD markings.
Failure Case: A 2024 Texas plant fire traced to non-ATEX compliant Division 1 lights melting under ethanol vapor exposure.
4. Cost-Benefit Analysis: Total Ownership Considerations
Initial Costs: ATEX Zone 1 lights cost 20-35% more due to precision machining, but reduce explosion-related downtime.
Maintenance: Division 1’s flame-resistant coatings require quarterly infrared inspections (per ISA 60079-17), adding $1,200/year per fixture.
ROI Example: A petrochemical plant switching to dual-certified LEDs reported 50% energy savings and 40% fewer safety incidents over 5 years.
5. Future Trends: Smart Technologies and Sustainability
IoT Integration: Zone 1-compliant sensors monitor methane leaks, triggering shutdowns in <0.5 seconds.
Bio-Based Flame Retardants: Lignin additives replace toxic brominated compounds, aligning with EU’s REACH regulations.